CONA SERVICES LLC DEPLOYS LYDIA VOICE
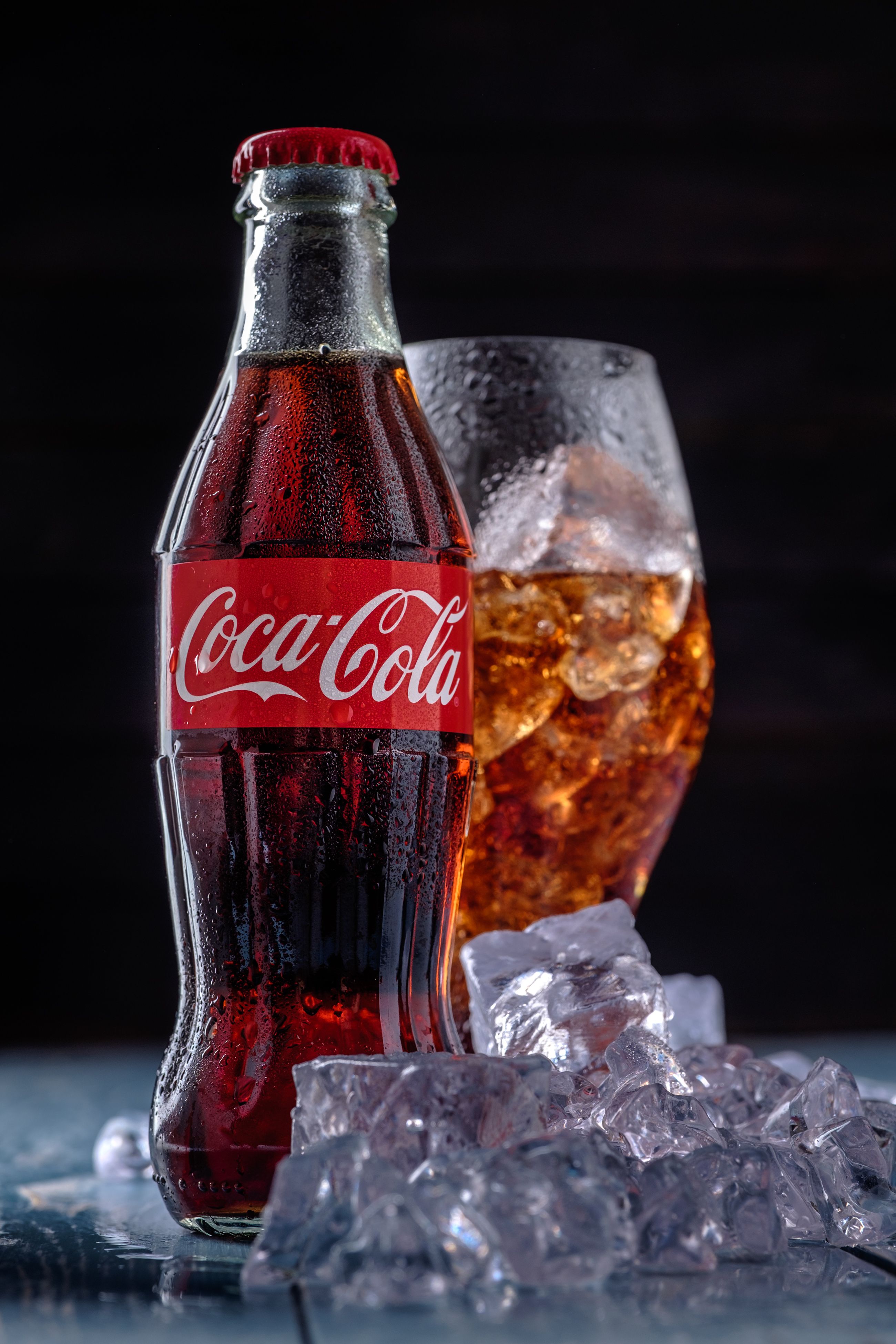
CONA Services LLC, a long-time user of voice-directed workflows, decided to evaluate a new voice solution in 2019 upon learning manufacturer support for their existing voice solution would be discontinued in 2021. The Atlanta headquartered organization — which provides information technology services for a dozen different North American Coca-Cola bottlers — saw this as an opportunity to take a fresh look at voice solutions currently available in the market.
According to Baron Jordan, CONA Chief Product Officer, Supply Chain, “Our previous voice system had a complex architecture and required the software to be hosted and run on individual servers at each deployment site.” Noting that more than 90 bottling and distribution locations were using the voice-directed system to facilitate picking, which required extensive support, “Further, there were inconsistent voice recognition issues with the old system that associates found frustrating.”
THE CHALLENGE:
BETTER VOICE RECOGNITION
AND HIGHER PRODUCTIVITY
Jordan and his colleagues’ wish list for a new voice-directed solution included simplified architecture optimized for SAP, a universally supported platform, and the ability to enable continuous picking in challenging network environments. CONA’s previous system used voice over internet protocol (VoIP) to transmit pick instructions, but was prone to weak or dropped connections. Therefore, CONA desired a solution that would permit continuous picking, independent of a network connection, should the WiFi signal be weak or lost.
“On average, many sites have seen approximately a 6% to 7% productivity improvement over our previous voice solution. In operations with thousands of users and thousands of hours this can provide very significant savings.”
Baron Jordan, Chief Product Officer – Supply Chain at CONA
TESTING THE OPTIONS
After eight months of investigation, the CONA team selected two providers of voice solutions and invited them to demonstrate their solutions in a side-by-side pilot. To gain the best understanding of how each solution would work in a typical bottler’s facility, as well as to gauge the user experience, Jordan’s team selected a test location where associates were already familiar with the existing voice system.
In December 2019, both prospective solutions were connected to CONA’s back-end SAP enterprise resource planning (ERP) system and fed live data. Associates were outfitted with headsets and mobile devices, then sent off to test the two options in their real-world environment.
The clear winner of the two systems tested was Lydia Voice from Ehrhardt Partner Group (EPG), a leading global provider of supply chain execution and voice software solutions. “The Lydia Voice solution addressed all of our needs and concerns, and had the best user feedback,” Jordan noted.
THE BENEFITS OF LYDIA VOICE
The Lydia Voice solution’s software integrates directly with SAP via a remote function call (RFC) without any middleware. This made deployment of the new voice solution across multiple bottler locations much easier.
CONA’s previous inefficiencies related to both voice template training and poor voice recognition. Lydia Voice’s deep neural network voice recognition eliminated poor voice recognition and the need for voice template training. Optimized for the noisy warehouse environment, Lydia Voice automatically recognizes more than 50 different languages and a multitude of unique dialects.
The solution is device independent, allowing the solution to interface with various Android mobile devices providing each bottler location the ability to select the devices that best suit their unique environment or preferences.
Furthermore, Lydia Voice Dialogue Designer provides an integrated development environment enabling Jordan and his team to independently create customized voice-directed workflow configurations without EPG technicians or developers. In CONA’s case, the voice application is used to build different types of pallets and print pallet tickets, he said. “It also allows associates to access a special menu with user directed commands for activities like announcing they are taking a break,” continued Jordan. “That automatically updates our backend ERP system to track overall time spent by associates, supporting engineered labor standards (ELS) productivity calculations.”
“The new system is much better, very prompt, very clear and it’s straight to the point. I like it!”
Warehouse Worker, CONA SERVICES LLC
PANDEMIC-PROOF PILOT
After the successful pilot test, CONA elected to roll out Lydia Voice to its first site in March 2020, with a 12-month deployment plan for 92 other North American locations to be completed by March 2021.
The EPG installation team was prevented from traveling to facilitate on-site deployment at most of the distribution centers due to COVID-19 travel restrictions and site safety policies. A hybrid implementation plan utilizing EPG and CONA staff to remotely support on-site bottler IT resources was developed and documented to meet accelerated delivery requirements.
Bottlers’ IT staffers — with support from CONA’s IT department — were able to handle a majority of the installation and commissioning, and EPG provided extensive remote support for the implementation, Jordan added, noting: “EPG was a great implementation partner and offered tremendous customer support.”
CONVINCING RESULTS
By delivering high service availability in challenging network environments and eliminating voice template training and voice recognition errors, the Lydia Voice solution has increased efficiency at each of the 92 implementation sites.
Further, many other locations that previously used paper-based pick lists to fill orders are now transitioning to Lydia Voice. Jordan added that among the overwhelmingly positive feedback he’s received from the bottlers, a typical comment is: “This is the best thing we have ever rolled out to the warehouse. Where has this been the last five years?”